高い品質を特徴としてきたはずの国内製造業だが、近年は品質不正や重大インシデントなどの発生が後を絶たない。本連載は、品質管理の枠組みであるトヨタ式TQMと、製造現場での活用が期待されるIoT技術を組み合わせた、DX時代の品質保証強化を狙いとしている。第1回は、その基礎となる「品質保証強化の4つのステップ」について紹介する。
2022年07月07日 07時00分 公開[株式会社アムイ 代表取締役 山田浩貢,MONOist]
1.本連載の趣旨
製造業において品質保証の強化は永遠のテーマです。現在も、大手製造業での検査不正問題や重大インシデントが発生している状況下にあり、これまでの現場の人間力に頼り、紙を主体とした道具で行っていた品質保証の仕組みは限界を迎えています。
そのため、企業のトップはIoT(モノのインターネット)、AI(人工知能)などを活用したデジタル化を急激に図ろうとしています。しかしながら、本来の品質管理の原理原則に立ち返り、品質保証体制を強化するための製品ライフサイクル全体の業務改善および組織の役割分担までを見直さなければ、局所的な対応にとどまり根本的な解決に至りません。デジタル化はあくまで道具であり、業務内容や組織体制も変えて行かなければ品質管理の両輪を回してくことはできません。
そこで本連載では、品質保証強化に向けて以下のポイントを重点的に取り上げていきます。
- 品質保証強化の4つのステップと対応すべき課題
- トヨタ式TQMの概念と管理体系
- 今後主流となるSDGs、ESG(環境、社会、ガバナンス)の要求事項にどう適合していくか
- 最新の技術(IoT、AI、デジタルツイン、etc.)による業務変革のポイント
まず連載第1回の今回は「品質保証強化の4つのステップ」について紹介します。
2.品質保証強化のステップ
品質保証強化のステップは4つの段階に分かれます。
第1段階、第2段階では「製造品質強化」を図ります。第1段階は「検査による品質保証」です。ここでは、良品を確保するために検査を厳重に行って、市場に良品を供給する考え方になります。最終工程での検査で不良を見つけるために、厳重な検査や不良品の取り換えにコストがかかる点に問題があります。
第2段階は「生産プロセスでの品質作り込み」です。生産工程における「標準化」を強化することで品質を確保します。いわゆる“自工程完結”により後工程に不良を持ち込まない考え方です。各工程で品質が保証されますので、ムダが極小化されます。それでも不適切な標準や規格、設計上の不具合などが発生する問題があります。
第3段階、第4段階は「設計品質強化」を図ります。第3段階は「開発・設計および販売サービスを含めた品質確保」です。ここでは、顧客の要求を設計にフィードバックして「品質機能展開(QFD)」を活用することで設計品質を確保します。
第4段階は「商品サイクル(商品開発から廃棄まで)を意識した品質保証」です。地球環境保護のため、ESGの環境配慮に適合し社会への貢献も考慮していくことになります。ここまでくると、製品ライフサイクルにおける企画、設計、生産準備、生産のサイクル全体に対して品質強化が図れます。図1 品質保証強化の4つのステップ[クリックで拡大]
3.品質保証強化における課題
品質保証強化の4つのステップでは、以下のような課題があります(図2)。
3.1 製造品質の課題
3.1.1 検査上の課題
多くの製造現場では外観検査による全品検査が行われますが、依然として目視による人でのチェックが主流となっています。このため、不良が混入すると複数の人によるダブルチェックを行うことになります。
また、全ての検査プロセスで全品検査は行われておらず、寸法計測などは抜き取り検査が一般的です。これも人による計測となるため、作業が追い付かない事態も発生します。さらに検査記録は紙での管理が多く、紙を基にPCにデータ入力する工数が発生し、データを基に解析を行うまでにタイムラグが生じます。解析のデータ作成に時間がかかり、本来行いたい解析業務の時間が取れないこともあります。
画像検査システムの普及により、見つけやすい不良の発見については自働化できつつありますが、これでも詳細までの不良原因の特定には至りません。そのため、疑わしきものはいったん不良と判定しておき、詳細な不良原因の特定までは人手での詳細検査による作業を待たなければなりません。
3.1.2 品質の継続保証における課題
検査記録として、製造ロットごとの製造条件や検査結果が一部しか残っていないことが多く、この場合良品として製造されていたかの判断ができず再検査や全回収になってしまいます。いつ、どの工程で、どの設備で、誰が生産したかは残っていますが、どのような製造条件で製造したのか、という詳細な条件が分からないことが問題になります。
3.1.3 クレーム発生時の対処における課題
顧客からのクレーム発生時には、品質保証部が要因解析と影響範囲の調査を行います。しかし、この際のエビデンスとなる製造記録、検査記録に紙が用いられていることが多いため、要因解析と影響調査は品質保証部門だけで実施できず、設計部門、生産管理部門、製造部門、調達部門を巻き込んで実施することになり時間がかかります。
現在は製造ラインの自働化により高速に物が流れて生産できるようになっており、工程内の検査で不適合とされた物はラインから跳ね出されます。跳ね出された物は、再検査や詳細検査を行い良品と判断されればラインに再投入されます。この再投入によって生産順序が変更になるため、先入れ先出しの順序性が崩れるためトレーサビリティーが難しくなります。
3.2 設計品質の課題
3.2.1 新製品立ち上げ時の課題
近年は開発期間が短くなり、品質特性の基準を十分にクリアできない状態で量産工程に入るケースが多く、新製品の立ち上り時期は不適合品の手直しや廃棄によるロスへの対応などでバタバタします。
設計品質を作り込む手法として品質機能展開があります。そこでは「品質表(QA表)」から「QC工程表」を作成していきます。この流れの中で試作をしながら、市場からの製品の要求事項に適合していくための品質特性を作り込んでいきます。現在は、この作業そのものが紙と人手の管理になっており、作り込んだ品質特性が製品品質のどれに強く関わっているかを設計者が捉えるのに時間を要しています。
3.2.2 品質の継続保証における課題
素材加工の工程は、季節によって、素材の配合条件や温度、湿度など良品を確保する製造条件が微妙に変動します。品質基準を確保するための製造条件は一律で設定していますが、現場では熟練工がカンコツを働かせて製造条件を調整し、品質を確保しています。製造ロットごとの製造条件の情報はほとんど記録されていません。
よくある話ですが、旧製品を改良した新製品が発売されても、過去の製造や設計に起因する不具合の再発防止が十分できていないということを聞きます。これは、後工程や市場に流出した不良に対しての再発防止だけにとどまっており、製造現場で日々起こっている不良の再発防止まで十分にできていないことが原因として挙げられます。
3.3 デジタル化に向けた課題
3.3.1 人+紙を主体とした道具に頼った管理
これまでは紙を主体とした道具で、生産現場や設計業務に携わる人間力に頼った管理が中心でした。これでは、組織全体による業務の最適化には限界があります。最近では、情報格差が激しく、組織がサイロ化しているとも言われています。
そこで、生産現場の各工程で発生した各種データを必要な人が正しく理解でき活用できる仕組みを作ることが重要になります。そして、下流工程の問題について、源流となる設計工程に引き渡して解決を図り新製品に反映させなければなりません。これらの課題解決のためには、IT、IoTに基づく最新のデジタル技術を取り入れた、人に優しい道具の活用による安定した良品生産の維持が必要なのです。図2 品質保証強化における課題[クリックで拡大]
4.解決の方向性
では、これらの課題解決に対して具体的にどう取り組んだらよいのでしょうか。まず、品質マネジメントの体系として「トヨタ式TQMの体系と管理上のポイント」を理解することが重要と考えています。
これは、「トップダウンによる方針管理」と「ボトムアップによる日常管理(QCサークル)」の両輪で成り立ちます。その考え方を理解することによって、組織的な品質強化につなげられるのです。
次に、製品開発(現行品、新製品)における管理のポイントとしては、QFD、故障モード影響解析(FMEA)、関数データ解析(FDA)、QC工程表の流れの効率化を図ることが重要です。これらにより製品開発プロセスの最適化が図れます。
その後の生産段階では、各製造工程の品質管理におけるリアルタイム解析と多角解析強化が求められます。そして、仕入先から製造工程を経て顧客までをつなげたサプライチェーンのトレーサビリティーの仕組みや、総合的設備管理(TPM:Total Productive Maintenance)との連携も品質強化のポイントとなります。
これからの時代、業務全般に関わるESGの要求事項に適合していくため、組織全般における業務の再設計が求められていますし、業務の効率化や迅速化、精度向上といった業務変革に対して、IoTやAI、デジタルツインなどの最新技術の活用が必須となっています。
筆者紹介
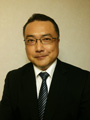
株式会社アムイ 代表取締役
山田 浩貢(やまだ ひろつぐ)
NTTデータ東海にて1990年代前半より製造業における生産管理パッケージシステムの企画開発・ユーザー適用および大手自動車部品メーカーを中心とした生産系業務改革、
原価企画・原価管理システム構築のプロジェクトマネージメントに従事。2013年に株式会社アムイを設立し大手から中堅中小製造業の業務改革、業務改善に伴うIT推進コンサルティングを手掛けている。「現場目線でのものづくり強化と経営効率向上にITを生かす」活動を展開中。